Concepts NREC introduces licensing for its new compact, high-speed, hermetically sealed turbogenerator. Nominally rated for 300 kWe, the CN300 is designed for converting low temperature heat to electric power using an Organic Rankine Cycle (ORC) process.
Historical Perspective
Increasing concerns for protecting the environment and the escalating cost of energy itself have raised interest in energy conservation to an all-time high. This interest extends to waste heat recovery systems. These systems produce electric power by converting thermal energy to electrical energy. And, when site conditions involve temperatures too low for conventional heat recovery systems, ORC processes become the best solution. These are typically defined as any heat source at temperatures below 800oF. In fact, according to one U.S. Department of Energy report, there could be as much as 1.5 to 2.0 quadrillion BTU/year of heat with temperatures below 500oF available from exhaust gas streams in the industrial sector alone. Naturally occurring heat sources may be just as plentiful.
There are estimated to be 400 ORC plants operating worldwide in the 250 to 50,000 kWe range. Of these, roughly 230 are in geothermal applications, and 170 are for industrial waste heat, biomass, or solar energy installations.
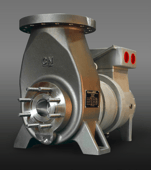
Figure 1 — The CN300, a 300 kWe integral turbine/generator unit.
Thermodynamic Background
The Rankine cycle is the primary thermodynamic cycle for generating the world’s electric power today. This is followed by the diesel (engine) and the Brayton (gas turbine) cycles. However, where the primary energy source for these cycles is coal, natural gas, or nuclear fuel, an ORC system uses a pre-existing heat source as its energy source and therefore does not typically require the use of any additional fuels.

Figure 2 — Simplified schematic of a Rankine cycle (courtesy of Wikipedia)
The Rankine cycle operates along the principles shown in Figure 2. A working fluid, typically water, is pumped (1-2) to a boiler to be vaporized into high-temperature, high- pressure steam (2-3). The produced steam then exits the boiler and enters a turbine (3), where it passes across the blades of that turbine. In the process, energy is transformed from thermal energy (temperature and pressure) to mechanical energy (rotating of a turbine shaft). The rotating turbine is then available to perform some useful work, such as turning a generator to produce electricity.
Upon exiting the turbine (4), the now-reduced energy steam passes to a condenser where it is cooled (condensed) back to the liquid state (4-1). From there, the water exits the condenser and flows back to the pump, and the cycle repeats.
Why the Organic Rankine Cycle?
In the classic Rankine cycle, several assumptions are made. One is that the boiler will have sufficient capacity to impart the thermal energy required by the turbine into the water.
At many energy recovery sites, however, this is not the case. Instead, the available heat source is at a much lower temperature than a conventional steam boiler, and so a conventional Rankine cycle using water as the working fluid will not work.
To be viable in lower temperature applications, an ORC system uses a fluid with a much lower boiling point than water. This lower-boiling-point liquid compensates for the lower temperature availability. Typical fluids include commercial refrigerants such as R125, R134a, R236fa, or R245fa and hydrocarbons, ammonia, and/or an ammonia-water mix. With one of these fluids as the working medium, the ORC cycle is able to
extract the thermal energy of a site and convert it into useful mechanical work. Such a low temperature conversion would not otherwise be thermodynamically feasible and/or economically practical using a conventional Rankine cycle process.
As the Second Law of Thermodynamics states, matching the temperature profiles of the waste heat source and the working fluid can reduce the exergy destruction (i.e., entropy increase) caused by having the temperature of the heat source closer to the temperature of the fluid that is absorbing that thermal energy. Such conformity between the heat source and the organic fluid-based heat sink markedly increases the amount of heat energy that can be recovered from the heat source, increasing the overall thermal efficiency of the unit.
The properties of organic working fluids also enable the expanded fluid to exit the turbine liquid droplet-free. This reduces erosion from impingement on the turbine airfoils.
ORC systems have several other key advantages. For example, whenever the source temperature is less than 350oF, the ORC may be the only commercially viable option. This is typical for many geothermal, amine generation, and refinery product streams. For source temperatures in the 350-500oF range, ORC performance generally exceeds that of a conventional Rankine cycle system. For any plant size below 2000 kWe, ORC systems are also far simpler to operate and maintain. Conventional Rankine cycle systems also require very expensive water treatment, additive chemicals, and non-condensable gas handling equipment.
As a final note, the Rankine cycle as a thermodynamic cycle is not restricted to any particular fluid composition, and the term “organic” is mainly a naming convention to indicate that the working fluid is something other than water. That is, whether it is an Organic Rankine Cycle or not, it is nevertheless a Rankine cycle and an ORC should not be regarded as a separate thermodynamic cycle or process.
Features and Benefits
The CN300 was developed specifically as an ORC energy recovery machine. It is a patent-pending, hermetically sealed design, with an ORC turbine and permanent magnet generator directly coupled that improves mechanical efficiency by up to 10 percentage points over conventional designs.
The CN300 turbine is a one-to-four stage, axial, impulse rotor-nozzle design configured in a subassembly cartridge arrangement. With its flexible flow path design, the CN300 can generate up to 330 kWe over a wide range of inlet conditions. It can also be customized by changing the aerodynamic shape of the turbine’s stages of rotors and nozzle stators. The basic design accommodates a wide range of turbine rotor and nozzle cartridges, while keeping the same housing and generator. Using a standardized turbine housing and generator this way eliminates most of the non-recurring engineering and manufacturing costs that would otherwise result from designing units to handle the multitude of heat recovery site conditions.
By using magnetic bearings, all of the cost, weight, space, interconnecting controls, and general complexity of an auxiliary bearing lube oil system are eliminated as well. The use of active magnetic bearings also means that the separate vibration probes and/or proximity sensors that would normally be required to monitor gearbox shaft vibration levels are also eliminated. The CN300 also has state-of-the-art electric generator drive controls. As a result, it doesn’t require an independent, electro-mechanical speed governor to safeguard against turbine overspeeding. Lastly, the hermetically sealed CN300 also eliminates the need for any shaft seals that keep the organic fluid within the ORC system’s closed loop piping.
The CN300 Design Process
The overall performance of any turbomachine is a function of its net efficiency. In the case of the CN300, this was optimized by doing what Concepts NREC does best: employing state-of-the-art aerodynamic and rotor-
dynamic analysis to create a simple and straight-forward engineering design.
Coupled with Design for Manufacturing principles, a low-cost turbine rotor-nozzle subassembly was produced. The aerodynamic analysis was done using Concepts NREC’s AxCent® software to model the continuous fluid flow as it expands through the turbine nozzles and transfers its momentum to produce torque at the output shaft.
The design also included in-depth structural analysis using finite element analysis, as shown in Figure 3. A final manufactured rotor is shown in Figure 4.
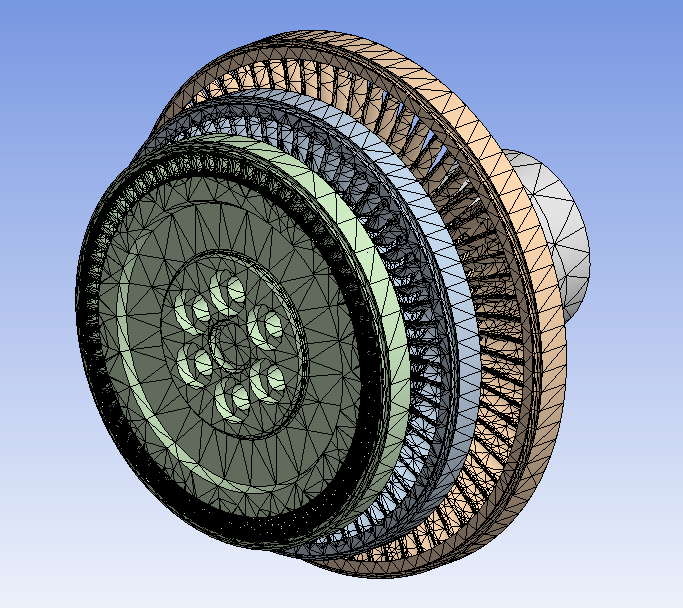
Figure 3 — An in-depth FEA analysis done on the CN300 rotor.
System Economics
The costs per kilowatt (kWe) and kilowatt-hour (kWe-hr) are greatly improved by designing the CN300 to operate at a constant 20,000 rpm. This optimizes the aerodynamic performance as well as the blade size and the ease of blade manufacturing. Likewise, the costs per kWe and kWe-hr are also reduced by eliminating the mechanical power losses and operating costs associated with shaft seals, mechanical bearings, a gearbox, and a pressurized lube oil system.
The installation costs, ranging from $1,000 to $1,200/kWe for a typical ORC system offered by others, can often exceed the cost of the ORC components themselves. The installed cost with a CN300, however, is minimal due to its low weight (1200 lbs.) and compact size (1.1m x 0.6 m x 0.9 m).
To learn more about the design plans and intellectual property available for licensing, please contact info@conceptsnrec.com.
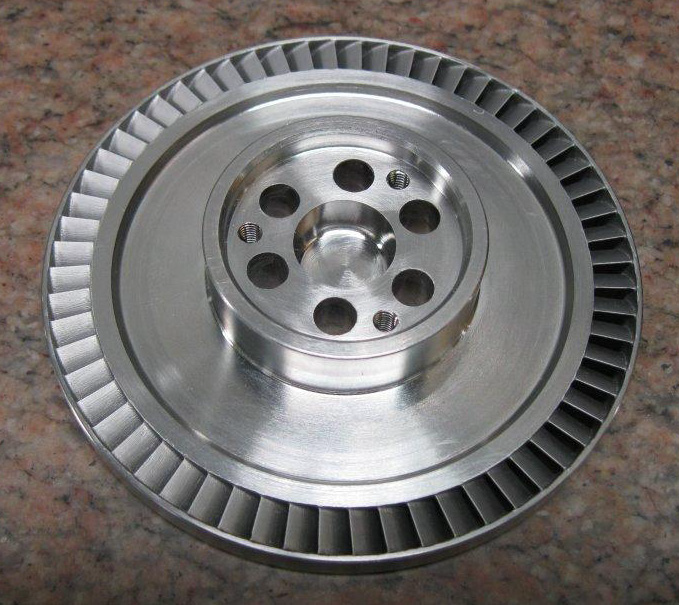
Figure 4 — A completed CN300 rotor (175 mm dia-meter).
Summary
Concepts NREC’s 50 years of turbomachinery experience culminates in the CN300 turbogenerator — an extremely attractive package for any waste heat recovery project with a low to moderate temperature waste heat source.
With its inherent flexibility, the CN300 offers more power and revenue for a given heat source, greatly reduced operating and maintenance costs, increased reliability, and a significantly smaller footprint than any other ORC turbogenerator available in the world today. To consider anything else for low temperature waste heat recovery systems could be an expensive mistake.
References:
1. “Waste Heat Recovery: Technology and Opportunities in the United States”; Report for the US DOE, BCS, Inc., March 2008.
2. “Waste Heat Recovery in Industrial Facilities: Opportunities for Combined Heat and Power and Industrial Heat Pumps”; EPRI, Palo Alto, CA, 2010.