Hydrogen is attracting a lot of interest in different circles these days from: propulsion, to energy storage, to personal transportation. The most obvious benefit of hydrogen fuel is a total lack of carbon in the exhaust products. This is rare for a fuel that’s a fairly high energy substance to begin with. More specifically, its high energy in terms of energy per unit of weight but somewhat less so in terms of volume.
Using hydrogen as a working fluid or simply moving it around from one place to another will require turbomachinery. Depending on the application, the fluid thermodynamic and fluid mechanical properties can usually be modeled quite simply. This is generally the case for near room pressure and temperature conditions. Other applications, like conversion to liquid for storage, require fancier models that can handle multiple phases. Despite the seemingly exotic nature of it, hydrogen presents no more of a challenge to model than other more mundane fluids like air and water.
In applications of moderate temperature and pressure, the real challenge is in the mechanical design. Hydrogen is, of course, the lightest element and low-density fluids require a lot of energy addition to realize a given pressure gain. High energy levels in turbomachinery means high velocities, and high velocities mean high stress levels in the rotating components.
To visualize the problem, take a look at the diagram below. The design on the right is a pressure ratio 2 compressor laid out in the meanline code COMPAL™, moving basic air. The design on the left is a hydrogen design of a similar pressure ratio using the same tip speed of the impeller as the air design. Tip speed is a good proxy for maximum stress levels. So, to reach the same pressure ratio, while maintaining the same material stress limits, we need 5 stages for hydrogen, where as we only need one for air.
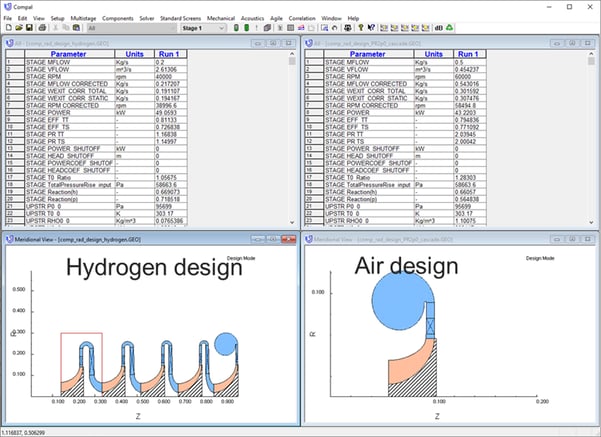
There’s nothing particularly difficult or complicated about the aerodynamic design process in this case. The same general design rules and loss models can be used for just about any fluid. Meanline codes might need a bit more scrutiny in these cases since the empirical data they’re based on tends to be weighted towards air. Otherwise, the process is very similar. The full 3D geometry, shown below in AxCent™, has a similar shaping and scale that we might expect from a more conventional air compressor.
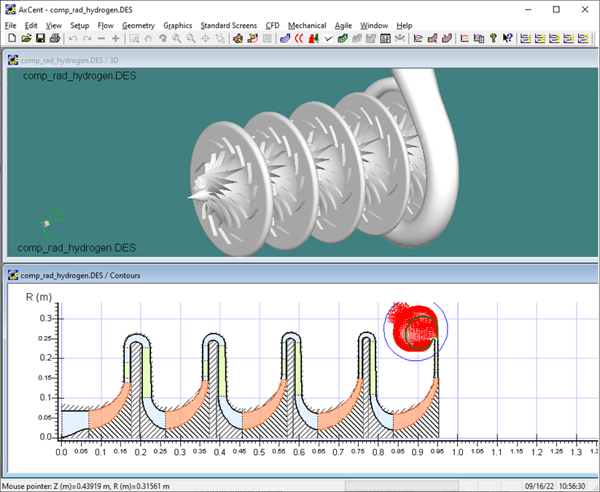
The cost and complexity of a 5-stage machine is obviously going to be a lot higher than a single stage. This being the case, the designer might want to push the usual limits of stress and make at least some aero compromises to reduce the stage number. Ultimately, as in all design exercises, there’s trade-offs between performance and costs that have to be made. A modern design system like Concepts NREC’s Agile Engineering Design System®, can greatly facilitate this process and get you the best combination in fastest amount of time.
We welcome your questions and comments here, or contact us at info@conceptsnrec.com for further dialogue.