Automated optimization is becoming more and more common place in the turbomachinery industry today. What was once exclusively the domain of academics and high-end researchers, has become much more widespread today. The rise of optimization is directly related to ever increasing computer power available and the advent of new software tools to set it up. Virtually every category of turbomachinery has adopted it, at least to some degree. One can find many examples of advanced optimization in the open literature but more practical applications can add value to your product line in a very reasonable time and effort.
The TurboOPT II software program integrates multi-disciplinary optimization with meanline or overall design through COMPAL®, PUMPAL®, FANPAL™, RITAL™ and AXIAL™, detailed design through AxCent®, and engineering analysis through FINE/pbCFD™, FINE™/Turbo, FINE™/Open and Pushbutton FEA™. It addresses compressors, pumps, fans, and turbines, including radial, mixed-flow, and axial machinery, or any combination thereof, with access to major input and output variables of the various codes and the Agile links through Python® scripting. TurboOPT II offers optimization layouts ranging from a single-disciplinary task to nested, coupled or combined optimizations. It includes an internal optimizer based on SciPy and the compatibility tools to seamlessly communicate with several commercial third-party optimizers.
Started in 1994 at Sandia National Laboratories, the Dakota project uses computational methods to simulate and optimize complex physical systems across many engineering fields. It provides a robust, open source interface to many different systems analysis methods that can be used alone or as part of a more advanced optimization strategy. To learn more about the Dakota project, please visit the website: https://dakota.sandia.gov/content/about.
The 2019 release of TurboOPT II introduced Dakota 6.9 as a built-in optimizer choice. Users can easily employ either/both of two pre-selected algorithms that are well-suited to many types of optimizations. The multi-objective genetic algorithm (MOGA) is the chosen global search that uses a more sophisticated function than the SciPy internal optimizer to determine improving solutions, especially when there are several objectives and trade-offs must be made. The chosen local search is a gradient optimization method (conmin). TurboOPT II converts the prepared optimization setup and exploration settings into a Dakota-ready model with the push of a button, while allowing advanced users to directly modify settings in Dakota input files before launching the optimization.
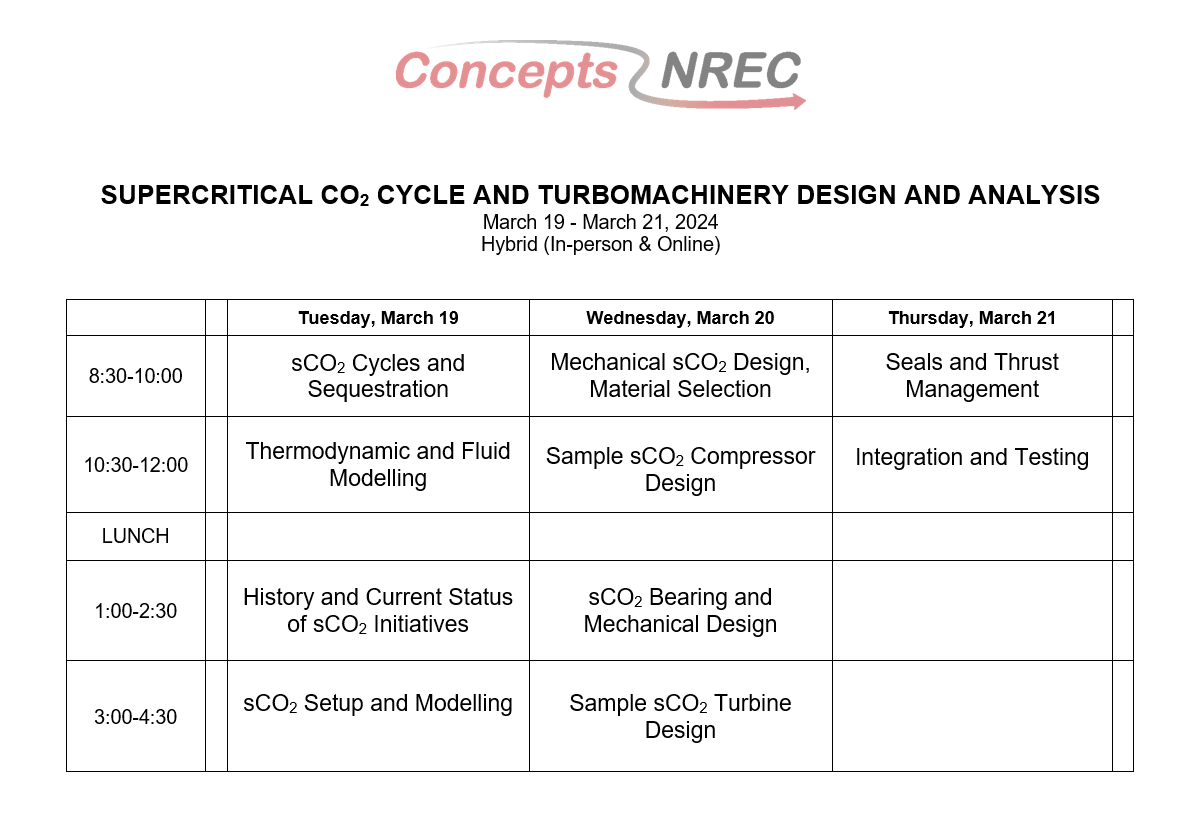
All solution details are fed back into the TurboOPT II user interface to show real-time history plots, tabular results, and performance maps.
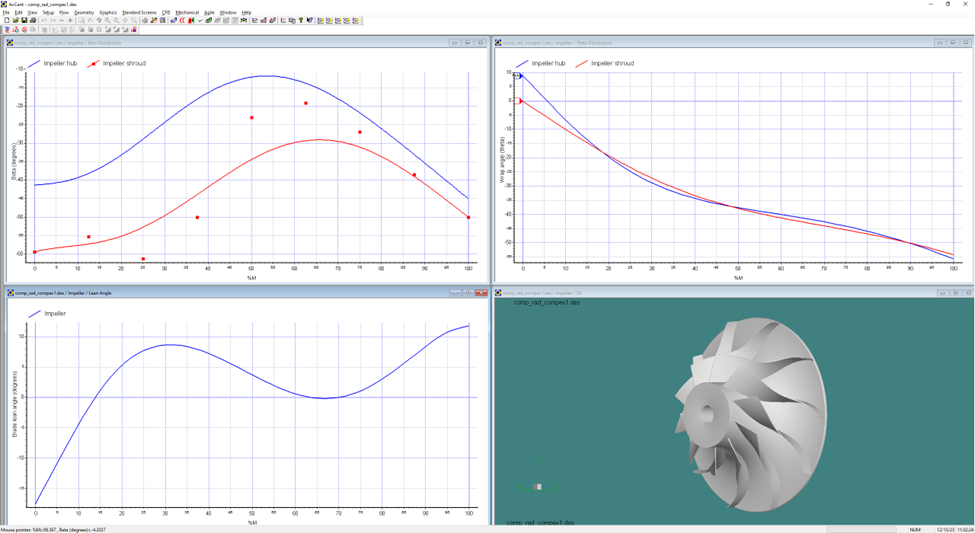
In addition to an automated setup and launch via TurboOPT II, the parallel capability of Dakota is exposed to the TurboOPT II user. This is an incredible time saver for engineers with available computing resources and serves to further shorten design cycles and reduce development costs.
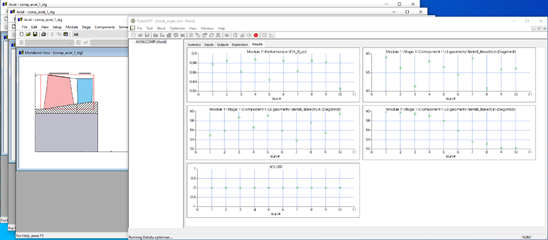
Here is an example of the Dakota optimizer and TurboOPT showing initial and improved AxCent geometries. The Pritchard blade design was run in parallel through AxCent’s blade-to-blade solver using Dakota’s global and local searches. A handful of nozzle and rotor geometry parameters were varied to maximize efficiency, keeping within the constraints provided in TurboOPT. A significant increase in efficiency was seen over approximately 250 iterations.
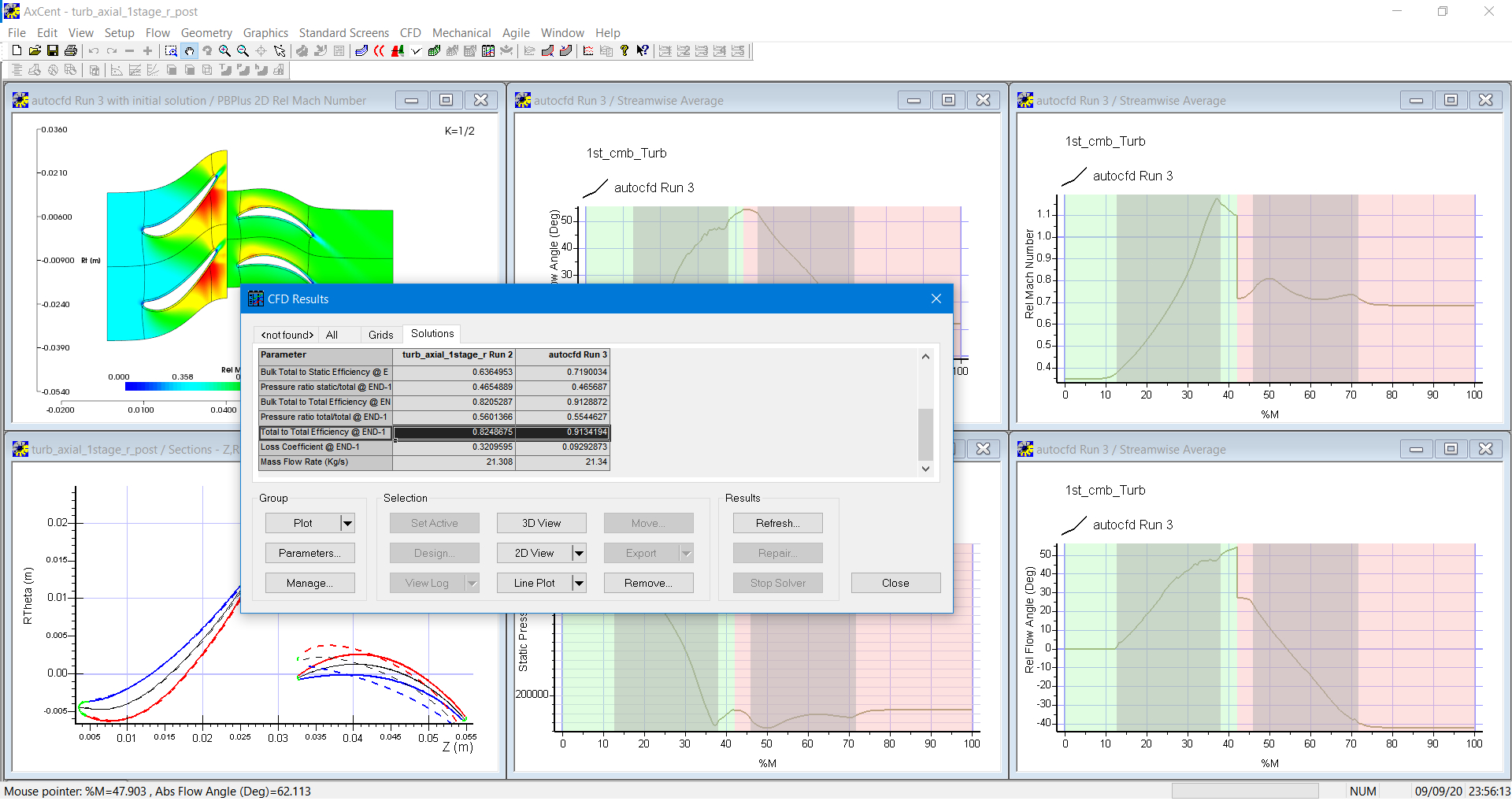
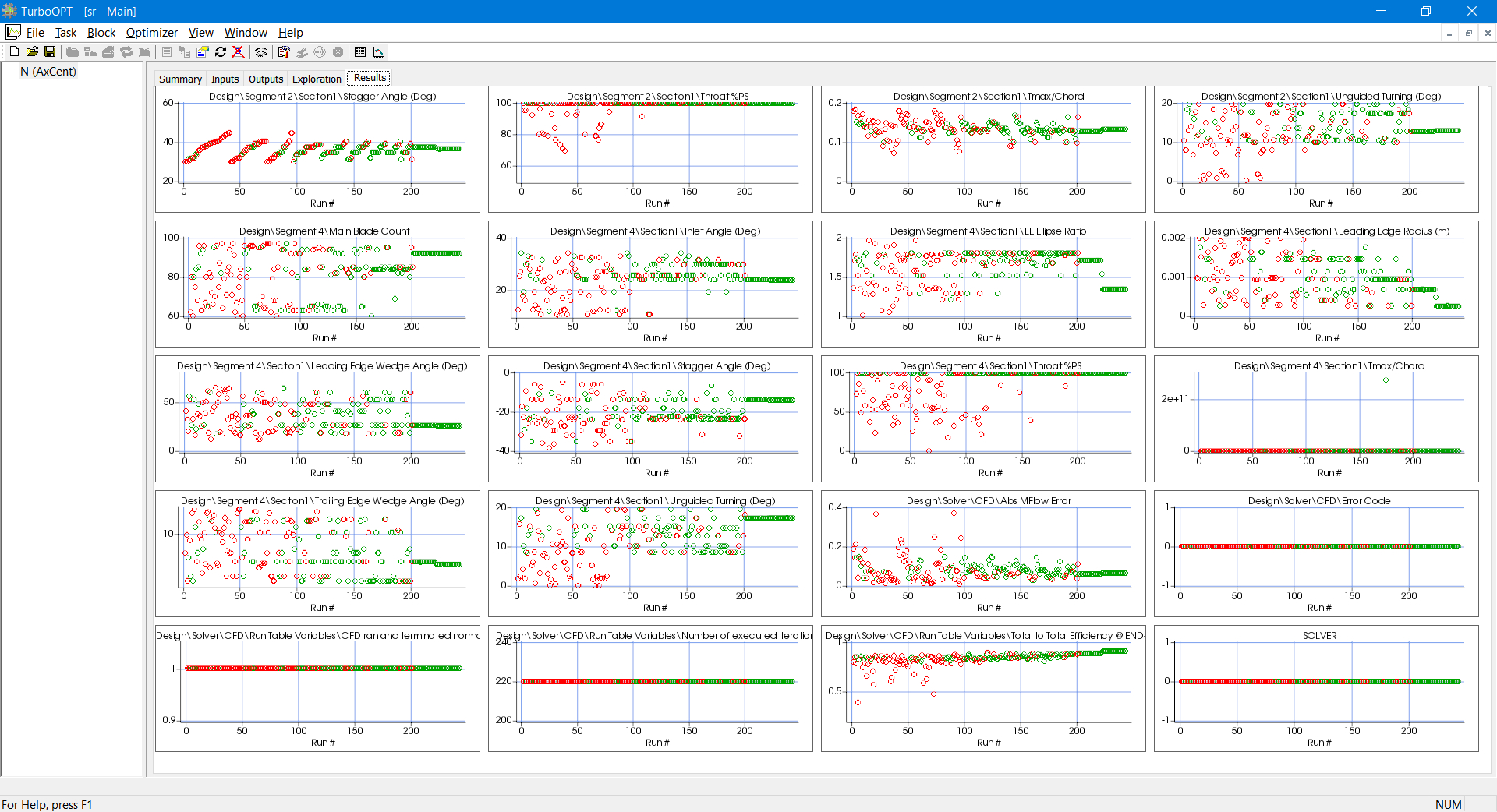
The Dakota optimizer is both a powerful and economical choice within the TurboOPT II application. TurboOPT’s built-in, seamless communication with Dakota gives the user easy and extensible means to tap into advanced optimization methods at no additional cost.