It is not a secret that when designing turbomachinery components there is a trade-off between the performance and durability. I challenge any aero or structural designer to highlight a geometric parameter, that when modified, is beneficial for both. Because of this trade-off, designers are often faced with the dilemma of selecting reduced performance or life when finalizing a component design. But which one should be sacrificed for the benefit of the other? This brings us to the all-important question: What is more important in turbomachinery design: performance or durability?
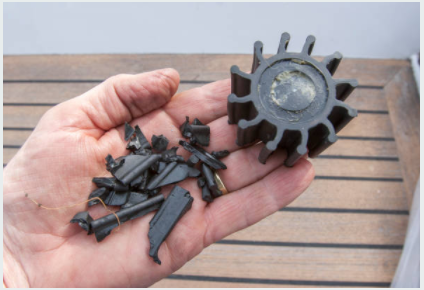
If you ask an aerodynamicist this question, they will undoubtedly say that their design must reach (or exceed) the specified (required) pressure ratio (head), efficiency, etc. On the contrary, if you ask a structural analyst this very same question, they will certainly say that their design much reach (or exceed) the specified (required) life. Full disclosure moving forward: I am a classically trained structural mechanics engineer. I will do my best to remain as unbiased as possible moving forward.
For every design, we accept that there is a desired performance and durability requirement that is developed to ensure that the machine can serve its purpose. Our assessment of performance is generally guided by efficiency, pressure ratio, power, or some other measurable output(s) at a given design point. Granted, there can be multiple operating points, and range may be the biggest concern for certain designs, and this can muddy the waters a bit with respect to performance requirements being met.
But what does “durability” really mean? There really isn’t a single design point output that can describe durability. In many cases, the term “life” will be used to describe durability. But what does “life” really mean? There are many different “lives” that need to be assessed. There can be low cycle fatigue (LCF) life that is governed by the changes in steady loadings on the component during operation (e.g. moving from one speed to another—“throttling” the machine). There are also high cycle fatigue (HCF) loads, commonly vibration, that impact life. In hot applications, there is also creep life that must be assessed. And in many turbomachinery component designs, there is no generalizations that can be drawn—they are all unique. That is, we can’t enter the structural design of a radial turbine thinking “all radial turbines are creep life limited” or that of a centrifugal compressor from the perspective of “all centrifs are HCF life limited”.
The prevailing sentiment to answer to our overriding question is almost born out of the common workflow for designing a compressor, turbine, pump, or fan. Think about it. Where does your company start when faced with designing a new turbomachine? I’d be willing to bet an irresponsible amount of money that you start with a cycle analysis (to determine your component inlet conditions) and meanline (1D) scoping to size your component. And I’d bet another irresponsible amount of money that you move directly to 3D blading, 2D analysis, and even 3D CFD or optimization to validate that your design meets its performance requirements before even running any finite element analysis (FEA) or completing any preliminary rotordynamics analysis.
If I’m wrong, then great! Your company understands the value of concurrent engineering of turbomachinery! Likely because lessons learned from past designs have proven that having tunnel vision on performance leads to a lot of lost time iterating on designs that are not practical. The trade-offs discussed earlier are the culprit leading us to these impractical designs. Now, I’m not saying that starting with a performance evaluation is a flawed methodology. But there should certainly be structural and rotordynamics evaluations completed at the onset to ground the design effort moving forward.
So now I will provide my answer to the question up for debate: durability is actually more important than performance. The simplest form of my argument is this: performance, any measure of which, goes to 0 if the component doesn’t stay in one piece. I will agree that seems like an oversimplification. However, at the moment of a structural/mechanical failure of the machine, it doesn’t operate anymore! A closer focus on durability can also minimize the variable costs of operating the machine. Better durability leads to longer overhaul periods, reduced spare inventory, less maintenance labor, and more (like never fully destroying a machine due to catastrophic structural failure!). Granted, reducing the performance characteristics will also have a cost, but they are not generally as costly as machine down time.
Let’s be clear: this question is supposed to invite a lively debate between aerodynamicists and structural analysts. We all know that performance and durability are both important. But we should all agree on this: it is really hard to characterize the performance of a machine that isn’t operational.
If you have any questions or comments, please let us know in the comments section below or contact us at info@conceptsnrec.com.