Why supercritical CO2?
Super critical carbon dioxide (sCO2) is one of the hottest topics in the turbomachinery world right now. From my own experience, I remember when the subject occupied a few sleepy sessions at the ASME Turbo Expo several years back. Today, its possible to spend the entire week at the conference and never leave a well-attended session dedicated specifically to sCO2.
There’s no shortage of explanations out there about what the inherent advantages of super-critical sCO2 cycles are. Some of these are rather difficult to follow, at least from a laymen’s perspective so let try a more intuitive explanation.
If you take the Carnot cycle efficiency has gospel (and there’s no reason not to!) you know the total efficiency cannot be greater than:
Cycle Efficiencymax = (Tmax – Tmin)/Tmax
This being the case, the actual efficiency is a function of the Carnot efficiency plus the fluid properties combined with the processes of the cycle. In general, it’s only practical to compress or expand a fluid in a nearly constant entropy process. Likewise, heating or cooling a fluid is only practical in a nearly constant pressure process. The figure below shows a Carnot and two slightly idealized cycles, a two-phase steam cycle in the middle, and a supercritical sCO2 cycle on the right.
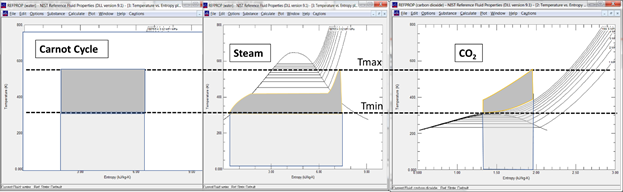
In simplified terms, the efficiency of the cycle is the dark gray area of the plots, divided by both the dark and light grey areas together. Carbon dioxide happens to have fluid properties that enable the sCO2 cycle to be closer to the Carnot cycle. In other words, sCO2 is able to “fill the box” better than almost any other fluid at least at temperatures and pressures that are easy for us to work with (again, this is rather simplified example that does not account for the complexities of regeneration or recuperating on the thermodynamics of the cycle). Another advantage is the energy capacity (specific heat in thermodynamic terms) of sCO2 is very high near the critical point and the net result of this is that you can produce a lot of power in a small system.
What are the issues?
Of course, if it was all that simple, everyone would already be doing it. The very high-power density, while ultimately an advantage, makes it very difficult to scale down to small power levels. For example, the most comprehensive test data to date is for a sCO2 compressor rotor not much bigger than a quarter. Pressure levels are also much higher (more than 80 atmospheres) than typical steam cycles and this requires careful design of the machinery and heat exchangers.
Beyond these practical considerations, there are core modeling issues for the design of sCO2 turbomachinery that are only now coming into focus. Some of these open questions are:
- Will the standard turbulence models used in CFD work in the super-critical flow regime?
- Are fancier nucleation models needed to determine how and when carbon dioxide changes phase? Are they needed at all?
- Will phase changes and bubble formation erode sCO2 compressors as they can for more typical types of pumps?
- How corrosive will sCO2 be and with what materials?
While, its still early in the game, there seems to be a growing consensus that these problems are not a serious concern or are at least manageable.
One issue that will certainly always be a serious problem, is the highly variable properties of fluids near the critical point (fluid at the critical point is not really a gas and not really a liquid). This requires special thermodynamics models to capture these effects when analyzing the fluid flow. Not only are the properties changing as they flow through the compressor, but the bulk properties entering the compressor will also vary as the cycle conditions invariably drift around. This shifting of inflow conditions has profound effects on the volumetric flow and choking behavior which greatly effects the range and performance of the compressor.
How to deal with these tough issues?
Tackling these problems requires a state-of-the-art software suite for successful design and analysis of such complex turbomachinery components. Concepts NREC was awarded a contract by the Department of Energy to upgrade the Agile Design System for effective sCO2 design. Special thermodynamic models were added to the code such as the NIST REFPROP models. The NIST models are considered a gold standard for thermodynamic modeling but computationally, they are very expensive. Concepts NREC has added special acceleration methods to these thermodynamic routines so that sCO2 design can now be conducted as quickly and as practically as almost any type of turbomachinery. Most importantly, modifications were made to the core flow routines to account for the significant differences in choking behavior that can occur at different point in the fluid state depending on the phase condition. All these models are compatible with our CFD partner Numeca in their Fine/Turbo and Fine/Open CFD solvers. Below are two figures, meanline and CFD, in the Fine/Agile suite using sCO2.
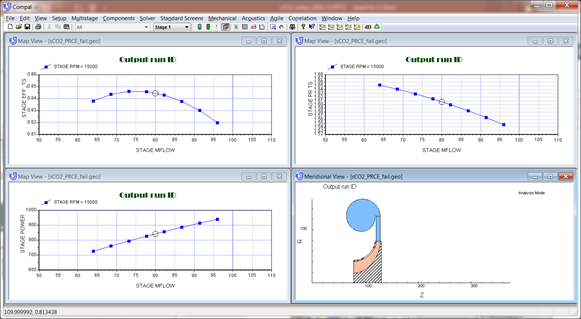
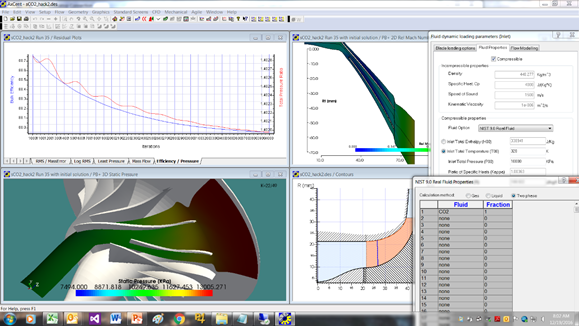
In summary, there are still significant challenges to be met in sCO2. Until more larger scale testing is done, we can’t be certain if the issues mentioned here will limit the effectiveness of sCO2 cycles or even if there will be problems that we haven’t yet contemplated. To determine this, several sCO2 initiatives are under way in many locations throughout the world. At several of these facilities, Concepts NREC software is an integral part of the design process and is playing a key role in the what could be the next generation of energy production.