The turbomachinery and software industries have evolved, in tandem, to high levels of maturity. On the engineering side, improved modeling capability and access to more powerful computational resources have revolutionized the design process, reducing costs and significantly improving performance and reliability. On the manufacturing side, additive manufacturing is starting to open up exciting new possibilities by allowing component shapes that simply were not possible before.
Like all technology, the evolution of these methods may seem clear enough for the near future, but it can be much more hazy over the long-term. Therefore, this article will take a look at what the future of turbomachinery software may hold.
The most advanced turbomachinery applications in the most performance-driven areas (i.e., propulsion and large scale energy production) have already reached the upper limits of what can be achieved by optimizing the primary flow path. For these industries, the most significant future improvements will come through upgrades to the secondary flow paths. This is particularly true in cooled gas turbine designs, where the extraction and re-injection of air has a major impact on cycle efficiency and local component performance.
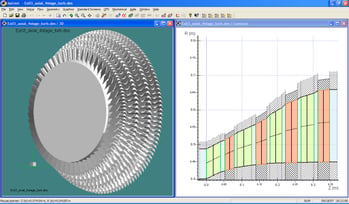

Figure 1 - Idealized representation of a high pressure turbine in AxCent®1 (left), and a more detailed figure of an actual turbine (right)
More complex shapes require more complex solution methods. The most obvious evolution of this in CFD and FEA has been the shift toward unstructured grids. As shapes become increasingly complex, they become progressively more difficult to capture with structured grid methods, whereas unstructured grids can effectively depict complexity. Figure 2 shows some of the grids that are possible today, in Pushbutton FEA™2 and in third-party CFD generators that can be imported from AxCent.
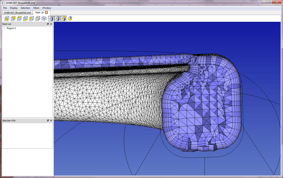
Figure 2 - Unstructured girds in PushButton FEA and in CFD from a volute shape exported from AxCent.
Lower order solvers, such as meanline and streamline curvature, will also evolve to capture these more- complex shapes and flow paths. The components in the secondary flow paths can be parameterized, just like the primary flow path, and their performance can be modeled accordingly. Some complicated iterations are often necessary, in order to ensure an overall balance of mass and energy. Eventually, the calculations begin to resemble more of a system analysis, rather than just a component analysis.
The other technology on the horizon that has the potential to powerfully impact the turbomachinery industry is additive manufacturing (AM). In many respects, the impact of AM will be felt more immediately in the design realm than in manufacturing; in fact, most industry experts do not expect AM to replace traditional manufacturing methods anytime soon. This is because the cost and quality of finished products are still major concerns in AM, and it is unlikely those issues can be quickly resolved.
Therefore, the primary benefit AM offers, at the present time, is the ability to make parts that simply cannot be made any other way. The flexibility of shapes made possible by AM opens up new design options that have never been considered before. AM’s potential is most significant in more complex, cooled parts, and some of these designs are already starting to enter the field.
AM’s ability to generate complex lattice structures with very high strength-to-weight ratios is another immediate appeal of the technology. Figure 3 shows an idealized rotor with a blend of lattice and solid cross-sections; it also shows an actual part, taken from a missile nose cone, which illustrates a similar application. A design like this would have significantly lower weight and rotational inertia than a conventional design, and also would have very different vibrational characteristics. Techniques like laser metal sintering and electron beam melting are giving rise to new shapes and options such as these, in a surprising variety of metals—including stainless steel, titanium, and high temperature nickel alloys.
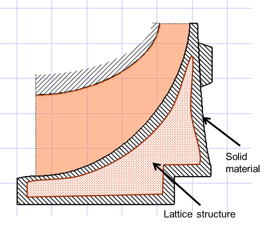
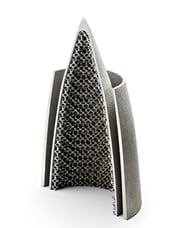
Figure 3 - Example of a rotor generated with additive manufacturing using a combination of solid and lattice structures (left). An actual nose cone of a missile using a similar method (right) Courtesy of Pratt & Whitney Additive Manufacturing Innovation Center, Univ. Connecticut
In order for the full potential of AM to be realized, the software industry needs to provide the next generation of tools to take advantage of this new technology. Such software will include more complex geometry generation, to lay out the interlocking structures, and will also include improved modeling methods.
Many of the more complex, smaller-scale structures possible in AM are too fine to be discretized directly using standard numerical methods, and must be solved as a macrostructure with the appropriate bulk properties defined. A lot of research is now being done to try to quantify these bulk properties for practical analysis. Residual stress levels in the parts produced, and defects in the structures that result from the more limited tolerances in AM, are major sources of uncertainty today. Surface finishes from AM-produced parts are also generally too rough for primary flow path components, and usually require finishing with a more conventional subtractive process.
Inevitably, advanced shaping will lead to advanced optimization processes. There are so many possibilities, and the potential is so open-ended, that it is hard to visualize exactly where AM might go in the future. Some tantalizing hints of the possibilities are starting emerge, and some of the designs are so unique and unconventional that they bear little resemblance to the items they are designed to replace. The potential of AM is limited as much by imagination as by technology. (One intriguing trend is the resemblance of these optimized designs to biological systems. For example, the lattice/solid structures often show a strong similarity to bone, and optimized flow passages resemble arteries and veins.)
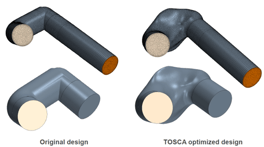
Figure 4 - Left—Fluid duct optimization using AM technology [courtesy of Ford Motor Company]; Right—Advanced bracket design [“Topology Optimization for Additive Manufacturing”, Brackett et al.; Solid Freeform Fabrication Symposium, 2015]
In summary, there are still many unresolved issues that need to be worked out in the next generation of turbomachinery modeling and manufacturing. A lot of work remains to be done before new methods can enter everyday service across the broader industry. But the potential for these methods is already starting to show up in the most demanding applications, and their presence will increasingly be felt in new areas. The ability to lay out, analyze, and optimize these new options in the next generation of software will be the key to their success.
1 AxCent is a registered trademark of Concepts NREC, LLC
2 Pushbutton FEA is a trademark of Concepts NREC, LLC