I was a firefighter (we never call ourselves firemen) for more than ten years. While this was only a part time, volunteer gig, I was a turbomachinery developer and modeler as my full-time job. Obviously, firefighters use all kinds of turbomachinery and I found it interesting to experience it from the user’s perspective.
Pumps are at the top of the list of turbomachinery tools that firefighters use. No surprise there. We had all kinds of pumps, but the common theme was high volume and moderate pressure. A discharge pressure of about 100 psi (about 690,00 pascals) was common for flow rates of about 150 gal/min/hose (9.5 lt/sec/hose). Flow rates are generally limited by how much force one firefighter could handle on a standard 1-3/4 in (4.4 cm) diameter hose, but one pump could feed as many 4 hoses at a time. Power requirements are quite high at these flow rates and pressures, so they generally require the full power of the truck engine to feed them.
There are two kinds of fire-fighting strategies: interior and exterior. Interior fires usually require only a few thousand gallons to finish off. Exterior fire-fighting is generally applied to larger fires where the process of putting “the-wet-stuff-on-the-red-stuff” is much less direct and efficient.
It’s not unusual to dump over 100,000 gallons (375,000 L) of water even on a run-of-the-mill barn fire in an exterior attack. All this volume requires many hours of reliable operation from the turbomachinery system.
Ventilation systems are also vital. Ventilation fans are not only used to expel smoke. They are critical tools to control the direction of the fire and bring the temperatures down to survivable levels for firefighters in an interior attack. A typical fan can move thousands of cubic feet of air per minute. Because the power requirements are much lower for fans than pumps, they can usually be handled by the truck’s electrical system or by a portable engine.
Because lives are on the line and these systems are not typically running day in and day out, the focus of firefighter turbomachinery is on reliability and range, rather than efficiency. The amount of power that can be brought to bear on the fire scene is quite remarkable. Our small rural town could have four heavy trucks on the scene in minutes with dozens more easily available on back-up from neighboring towns. Lack of power is rarely a problem on the fire scene, which makes efficiency that much less of an issue.
Occasionally my two roles intersected. Concepts NREC designed a firefighting pump for the Coast Guard that was driven by a two-stage gas turbine engine.
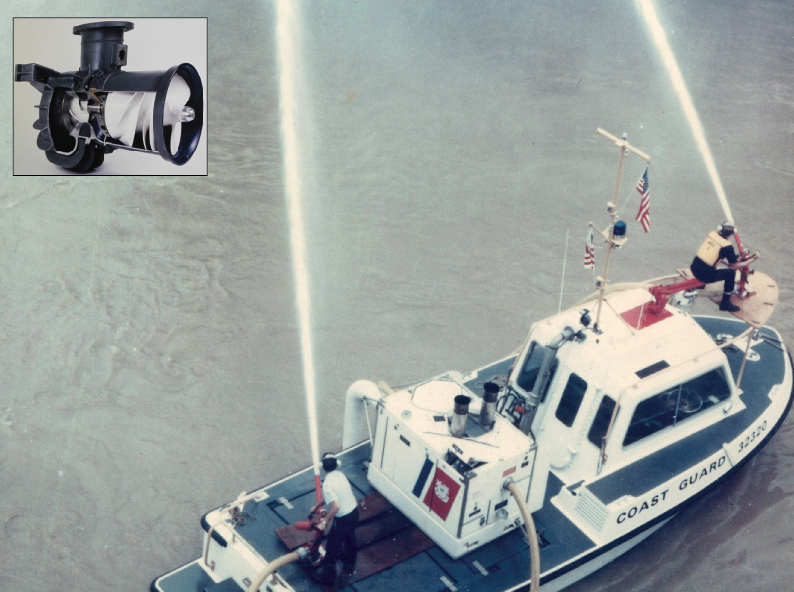
It was used to fight fires at sea and needed to reach large ships from the relatively low Coast Guard boats. Specs included 180 psig discharge pressure at 2,000 gpm, 6,680 rpm, and 10 feet of suction lift. It moved a lot of water!
I also trained an engineer from a firefighting equipment company on our turbomachinery design software. Often times, while fighting a fire, I wondered if I had a hand in the development of the turbomachinery systems I was depending on.