Today, however, given the world’s general engineering knowledge base on implementing more efficient engine cycles, serious consideration should be given to these other cycles, bypassing the traditional GG cycle first step when starting out new in rocket development. The DE cycle is one example that should be considered for a lower thrust cryogenic fuel application such as liquid methane or liquid hydrogen. The DE cycle has the overall benefit of higher specific impulse (for a given fuel) and lower gas temperatures for easier reusability, which is of growing concern in today’s market.
To more easily compare the two cycles, the table below summarizes the pros and cons of each cycle from the perspective of the TPA design.
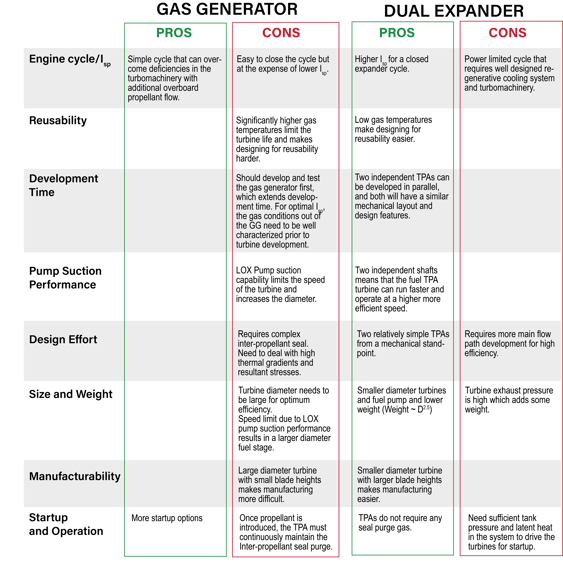
As seen in the table, the DE cycle has several advantages with respect to the TPA in terms of reusability, development time, pump suction performance, design effort, size and weight, and manufacturability The turbomachinery for the DE cycle needs to have the highest possible efficiency to close the cycle, but high efficiency turbomachinery is something that Concepts NREC is well known for and has been doing for over 60 years. As you develop your rocket engine architecture, please don’t hesitate to reach out to us for help with the turbopump design and manufacturing. We have good experience in both areas and can show you the best approach for the turbopump component or supply you with the software and tools to do the design work yourself.
We invite you to register for the 35th Annual Small Satellite Conference and visit us there online August 7-12. This conference brings together the best-of-the-best in technology support providers for propulsion and launch specialists to explore the realm of the possible in new space mission operations. We’ll be offering a software demonstration Tuesday, August 10th, 3pm-5pm MST on “How to Design Your Rocket Turbopump with CAE and CAM Software Solutions”. On Wednesday, August 11th from 12-3pm MST, Kerry Oliphant, Senior Program Manager/Corporate Fellow and Mark Anderson, CTO, will host open hours for dialogue. Bring your questions for our experts!
If you have any questions or comments, please let us know in the comments section below or contact us at info@conceptsnrec.com.