Here at Concepts NREC, we work on a wide range of turbomachinery components designed for fluids ranging from gases to liquids, including supercritical fluids like supercritical CO2 which have properties of both gases and liquids. We do a lot of pump design, consulting work and education. In fact our annual course on Centrifugal and Axial Pump Design is consistently one of the most popular. Many engineers in the gas compressor industries consider pump design plain vanilla, without the added complexities of Mach number effects, but there are reasons why our pump course is so popular – pump design can indeed be very difficult, with a number of complicating factors that are unique or especially critical to the pump industry.
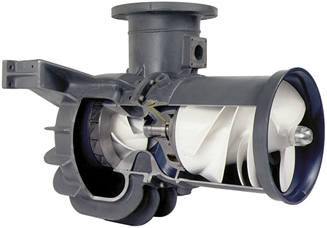
Arguably the most complicating factor in pump design, relative to other turbomachinery, is the risk of cavitation. Not all pumps are subject to installations where the available inlet head (often referred to as the net positive suction head available, or NPSHa) is low, but many are, and must be carefully designed to minimize the risk of cavitation. The design changes needed to minimize cavitation risk range from the correct sizing of the pump first stage inlet, to the design of the pump blading itself, with special consideration given to the blading near the inlet, sometimes referred to the inducer section. Indeed, some pumps require a separate inducer for the sole purpose of minimizing cavitation risk while slowing increasing the pressure in the pump so that local static pressure rises sufficiently above the fluid vapor pressure, allowing downstream components, from the first stage exducer on downstream, to be less prone to cavitation. This cavitation risk has led to a whole series of design techniques to avoid cavitation, and this cavitation avoidance leads to the first stage of multistage pumps often looking considerably different than downstream stages.
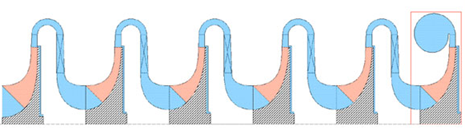
Another complicating factor in pump design is the higher radial and axial thrusts associated with the higher density fluids being pumped, as compared to many gas compressors. Capturing the higher axial thrust in pumps can be problematic due to restrictions on size and capacity of thrust bearings. There is then a resulting need to lower or minimize axial thrust, leading to a whole series of tricks the pump designer can use to reduce the thrust. These changes often come at the expense of pump performance, so the pump designer must carefully balance performance needs with mechanical and durability needs when axial thrust is a problem. Some of the pump design features that have arisen due to the need to control thrust include pump-out vanes on the backface of the impeller, scalloped impeller backfaces, and even holes through the impeller itself connecting the pump inlet to the pump backface to allow for better pressure balance and hence thrust balance.
These are only two examples of pump design challenges. Other issues such as leakage and leakage control, high radial forces, increased disk friction, etc. can be magnified in pump design relative to compressor design, all leading the pump designer to dig into their bag of tricks and make certain design choices and tradeoffs.
Gas compression designers should be relieved that they do not have to deal with design problems as shown in these pump examples, and indeed pump designs can be very challenging for these and other reasons. While fundamental physics still of course apply in pump design, it’s the bag of tricks that have been developed over years of design and trial and error testing that are of greatest interest and use to pump designers.
If you would like to learn more about these pump design issues and how to overcome them, considering attending our pump design course. Centrifugal and Axial Pump Design is coming up in a few weeks and is still open for new attendees. We spend a lot of time on cavitation, understanding what causes it and how to design for it, and we also spend significant time on axial thrust mitigation techniques, as well as many other topics.
If you are reading this blog after our 2020 course has been given, consult our website to see the current course schedule. We also can design and conduct custom education for your company at any point during the year, or consult directly with you on your design challenges, either through engineering consulting or providing appropriate design software.
#pumps #pumpdesign #turbomachinery #conceptsnrec