Can you really get something for nearly nothing? In many cases, a properly-designed compressor casing treatment can extend compressor operating range without having to pay an appreciable efficiency penalty. Major automotive turbocharger OEMs have been leading this design effort for years and have successfully gained compressor operating range increase on both sides of the compressor (pressure versus flow) map. In most cases, the range increase has outweighed any efficiency penalty and best of all, these so-called “ported shroud” designs are naturally uncomplicated to implement, meaning that incremental cost is low.
This technology is fairly low-impact to adapt to existing designs because it usually requires only a small change to the compressor inlet housing. These changes are usually slots or holes in the stationary part of the compressor, attached to a passage upstream. The idea is to remove the high-loss fluid from the outer periphery of the flow path and reintroduce it upstream and give it a chance to behave better the next time through. This passive removal of the high-loss flow allows the remainder of the flow to achieve orderly procession through the compressor, but also introduces the smallest amount of efficiency loss due to recycling of flow. However, the fluid traveling through the system can move more smoothly to lower-flow ranges than was possible in a baseline configuration. There are even a few cases where these lower-flow ranges are more efficient than expected. That is truly getting something for nothing! And, based on the manner and location of the removed flow, higher flows than were possible in the baseline can be seen. However, this higher-flow range is subject to a more cutthroat “increased range equals reduced efficiency” criteria.
Automotive turbocharger compressors are usually the types of compressors that need the most range. This need reflects the very demanding and inconstant conditions that automobiles must operate under. Consider the wide range of temperatures, from freezing cold winters to sweltering summers, not to mention that variations in altitude or varying driving speeds and styles. A single machine (turbocharger compressor) is asked to accept these variables of temperature/elevation/driver style as input, yet maintain an output of a relatively constant set of conditions to the engine. This results in a compressor operating map which must be extremely wide.
It is obvious why vehicles use this technology. The question is, can benefit other market segments? The answer is yes, since we know that there are very few compressors run at strictly-defined operating points and most have at least some variability in flow conditions. Designers of these other types of compressors have another option. Instead of strict control systems to ensure the compressor does not run into damaging flow ranges, they can explore a casing treatment that offers a low-cost, low-penalty method to gives them something for (nearly) nothing.
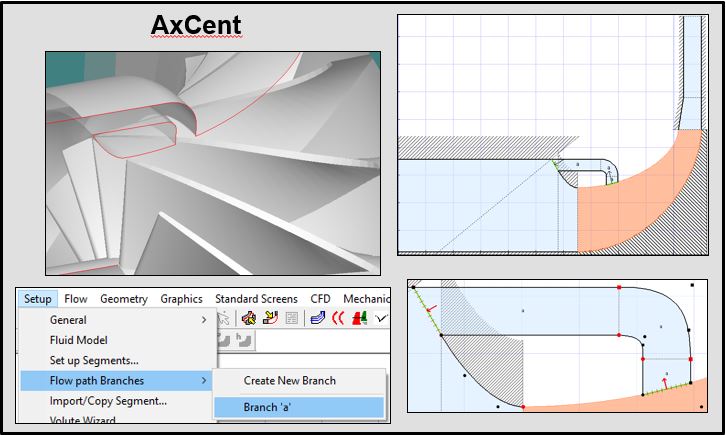
Concepts NREC’s latest 2017 Release of our Agile Engineering Design System® software enables this type of casing treatment to be designed and analyzed, from preliminary conception through 3D geometry creation and CFD, using Numeca’s FINE/Turbo. Optimization can also bring ported shroud designs to even higher levels of performance. Contact us to learn more.