A small turbine (for ORC, air liquification processes) , operating with low volumetric flows at inlet and significant pressure ratio in a single stage configuration (to reduce costs) is often associated with flow of media with transition from liquid to gas-liquid state, with operating levels of Mach numbers above 1.8 at nozzle exit, that assumes convergent-divergent nozzle geometry, and may require partial admission.
Low reaction stage partial admission design helps in achieving acceptable blade heights of manufacturable size. Preliminary design approach for best power generating cycle efficiency is already illustrated in previous blog discussions, which are focused on turbines operating with single phase flow, or flow with transition from gas to gas-liquid flow, dominated by presence of gas phase by mass and flow. That can be found here:
https://www.conceptsnrec.com/blog/coupled-optimization-of-preliminary-geometry-of-two-stage-low-flow-turbine-and-regenerative-rankine-cycle-parameters
https://www.conceptsnrec.com/blog/coupled-optimization-of-preliminary-geometry-of-two-stage-low-flow-turbine-and-regenerative-rankine-cycle-parameters-2
In the case of turboexpanders with liquid flow at inlet, additional complexities appear during executing preliminary design. Transition from liquid to gas-liquid mixture is a physically complex process, but in many preliminary design considerations, simplified modeling by assuming homogeneous equilibrium flow is a good starting point. Homogeneous equilibrium flow means two things:
-
Gas and liquid phases are present as structures of significantly smaller size than major dimensions of the flow passages, these structures are uniformly mixed, and move with the same velocity and acceleration
-
Heat and mass transfer processes between gas and liquid phases are completed instantaneously, it is further simplified by assuming temperatures and pressures in liquid and gas structures are the same.
The above assumptions allow direct use of common real gas thermodynamic libraries, such as ASME STEAM or NIST REFPROP with conventional “single phase” 1D-3D solvers. Yet it is often a challenge to expand operation of single-phase solvers on liquids with transitions to gas-liquid domain. There are practical challenges to be addressed for such simulations.
One challenge is that real gas models often do not report viscosity and sonic velocity values in 2-phase domain, required to assess choked flow and losses for predicting flow capacity and performance. Report from NIST REFPROP for Methane shows this problem:
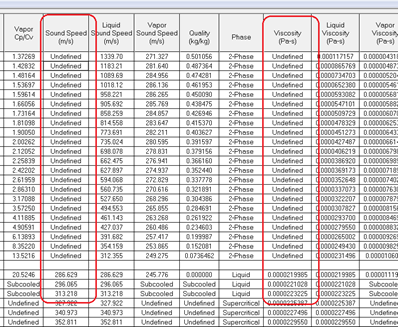
The second challenge is that huge variations in sonic velocity and density increases numerical stiffness of the models, and that requires special care to achieve robust convergence. Sonic velocity variation in the plot for water-vapor mixture (Semenov, Kosterin, “Results of studying the speed of sound in moving gas-liquid systems”. Teploenergetika, 11(6), 1964.) shows 2 and more orders of magnitude change for sonic velocity in transition from liquid to gas-liquid state.
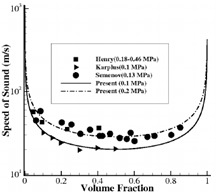
These complexities are considered and resolved in AXIAL™, permitting execution of preliminary designs of turboexpander turbines for CO2, N2, H2, O2, Methane, H2O, and others.
For example, let us consider a turboexpander design for Methane (ie case related to LNG) with the following conditions:
Mass flow: 5 kg/sec Inlet P: 320 Bar
Inlet T -50 degC Exit P: 5 Bar
Executing preliminary design targeting low reaction operation at design points produces geometry shown in the screenshot below. An example how execute and optimize preliminary design of choked flow low reaction turbine for best efficiency is described in
https://www.conceptsnrec.com/blog/preliminary-sizing-of-supersonic-turbines-with-partial-admission-for-best-performance-using-axial
If required, optimization of a turboexpander can be executed to maximize liquid content for a standalone machine or in coupled consideration with a relevant cycle.
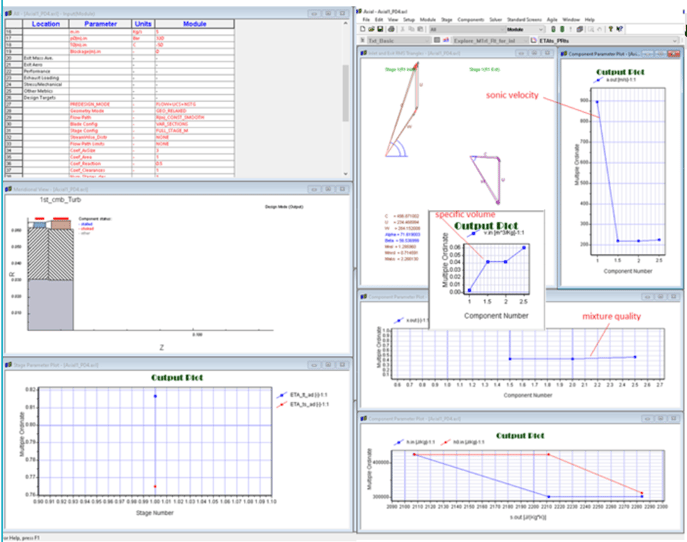
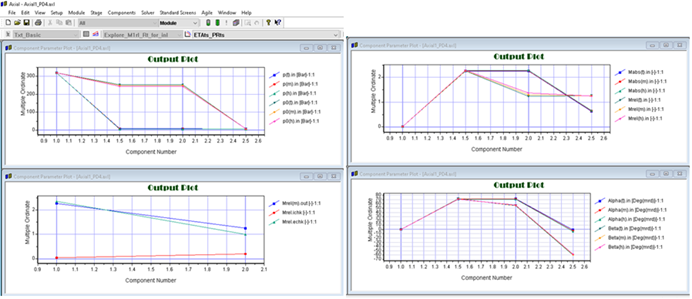
Preliminary design can be taken from AXIAL™ to AxCent® with blade profiles refined using B2B and 3D CFD solvers. Homogeneous equilibrium assumption for real gas media is compatible with single phase CFD solvers (H,P, Rho,C /W) formulation, but keeping numerical stability during run time may require adjusting stepping parameters beyond recommended ranges .
For example, selecting convergent-divergent nozzle and rotor profiles from the available library gives initial 3D geometry, with nozzle and rotor geometries initially refined using B2B PbCFD, run with real gas NIST REFPROP tables for Methane:
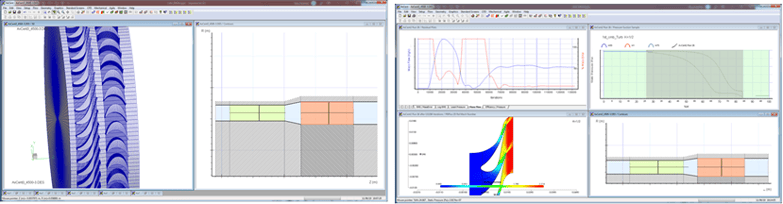
3D CFD using NUMECA (integrated with AxCent®) with condensable fluid properties also allows running flow analysis to acceptable convergence:
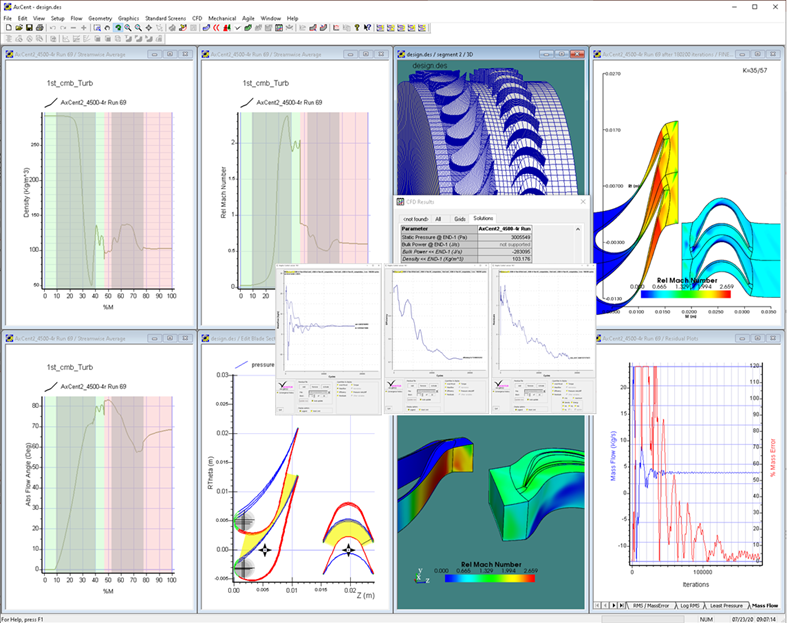
The required run time for liquid to gas-liquid flow in non-specialized real gas CFD solvers may be significant, approximately increased by factor [sonic velocity in liquid]/[minimum sonic velocity in gas-liquid mixture] vs conventional single phase calculations , due to need to keep numerical stability.
With the all above - the task of producing preliminary and 3D design for liquid to gas liquid expander turbine is resolvable numerically using Agile™ Design System. While there are several challenges designing with two-phase flow, the homogeneous equilibrium assumption can be used to bring the effort down to something on par with conventional single phase design. Additional test rig data can be used to calibrate the models further and some variation of the adjustable geometry parameters maybe necessary to finalize the design. If peak performance is not of primary concern of the turboexpander design, implementing design features to adjust geometry per measured field data (for example by using adjustable partial admission, or inlet valve control, or variable nozzle geometry) may help to deliver practical designs with reduced design effort and development costs. #turbomachinery #turbine #turbinedesign #conceptsnrec