High-efficiency, low-cavitation pumps often require a screw type inducer to treat the inflow to the main radial/mixed flow pump blades. Efficiency and head rise, split between inducer and main pump, are questions explored during the design process. Another important design consideration is the tolerance to cavitation. Finding the best solution, when there is often a trade-off between two or more operational conditions, is difficult. We have found that multi-objective optimization, for single or multiple operating points, is the best tool to use.
An example study: The 3D geometry variations of a screw inducer, looking at the trade-offs between efficiency and head rise (that affect head rise in the main pump), at fixed volumetric flow and inlet eye to the inducer.
Problem:
Freezing the inlet eye in the screw inducer and given volumetric flow - allowing arbitrary blade angle variations, hub contour variation, and inducer axial length - run a 3D CFD optimization to find geometries with the best efficiencies, while attempting to maximize inducer head rise.
The overall problem formulation uses 16 input parameters:
- 5 control points for hub contour between inlet and exit of the inducer
- 4 control points at inducer tip
- 5 control points at inducer hub, inducer axial length stretch factor
- TE lean angle
There are 9 constraints
- Range of interest for head rise
- Minimum hub separation
- Minimum allowed lean angles (negative) for the inducer blades
- Maximum allowed lean angles (positive) for the inducer blades
- Solidity (for reasonable blade loading to guarantee better cavitation stability)
- Grid generation status
- Solver success status
- CFD success status
- CFD convergence status
As well as two objective functions: Head rise and inducer efficiency
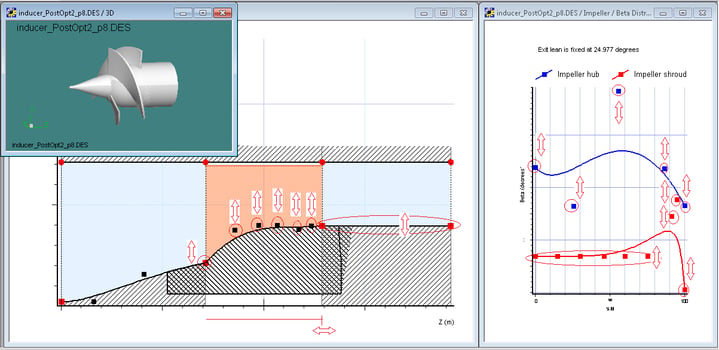
Figure 1. Geometry controls, exercised during inducer optimization
To run the optimization, we used AxCent®, TurboOPTll™ and a 3rd-party optimizer to execute parallel optimization on multiple computers.
To obtain both branches of the Pareto front, for the trade-off between efficiency and head rise, we needed to execute 2 optimization runs on both sides of the head rise ranges in relation to the best efficiency case.
The approximately 2400 geometry iterations are summarized in this plot:
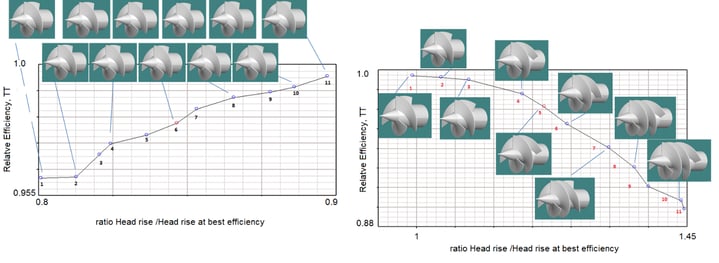
Figure 2: Results of optimization
Optimization results produced two distinct geometry patterns. One was dictated by the influence of blade loading in the high head rise domain, and the other by cavitation-friendly solidity in a low head rise domain.
Optimized solutions from the low head rise domain, which were limited by the condition to support the minimum required solidity (to get acceptable cavitation stability), show an almost constant axial length of the inducer with a trend to reduce efficiencies with the reduction of head rise.
Optimized solutions from the higher head rise range show an aggressive increase in the inducer axial length with rising heads. The solidity levels are high because longer blades are required to keep blade loading at clearance effects in check.
Looking at the combined inducer and pump optimization in the above example, you can see that there are many options depending on the various tradeoffs. Designers will have to decide which works best for their application, based on efficiency, head rise, cavitation, etc.
Using the best available tools, a design engineer will be able to create the optimum pump geometry with a screw-type inducer that takes into consideration design and off-design performance, sensitivity to cavitation inception, coupled with thrust and structural calculations. Tools that are able to deliver multi-objective optimization, for single or multiple operating points, deliver enormous timesaving benefits as well as superior results.