When starting a turbomachinery design, the first choice an engineer has to make is the thermodynamic model. The actual fluid type (air, water, R1234ze, etc) is usually clear enough, but what model approach should be selected? Looking at the fluid dialog in Concepts NREC software shows a myriad of options to choose from.
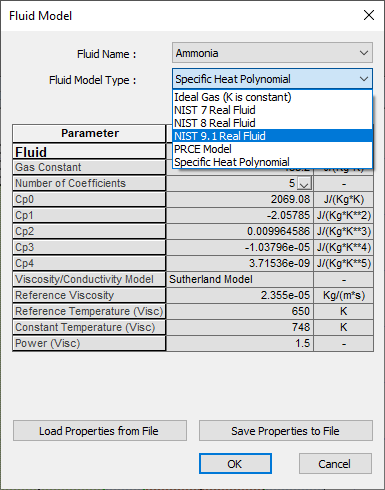
The answer depends on the fluid behavior in the region where you need to model it. Virtually any substance will behave like a simple perfect gas in some pressure and temperature region and likewise will exhibit totally different behavior in another condition. It is a misconception that fluids like air and argon are “perfect” gases while more complex molecules like refrigerants are “real” gases. In reality, both will show either behavior depending on conditions they exit in. What is true, in practice, as that refrigerants tend to be used in actual applications where they show real gas behavior. Likewise, substances like air behave very much like perfect gas in conditions we’re more familiar with, like the air you’re breathing now.
Some very nice primers on various thermodynamic models can be found in the blogs series:
https://www.conceptsnrec.com/blog/when-perfect-is-good-enough-perfect-gas-models
https://www.conceptsnrec.com/blog/fluid-phenomena-primer-energy-versus-temperature-specific-heat
https://www.conceptsnrec.com/blog/whats-better-than-perfect-semi-perfect-gas-models
https://www.conceptsnrec.com/blog/phase-change-make-mine-double
https://www.conceptsnrec.com/blog/fluid-modeling-liquified
https://www.conceptsnrec.com/blog/going-through-a-phase-modeling-phase-change-with-cubics
https://www.conceptsnrec.com/blog/non-equilibrium-modeling
Like most things, the best thermodynamic model to choose depends on a balance between cost and benefit. Models like perfect gas have almost no computational overhead or stability issues and are “perfectly” fine for many common fluids at moderate temperature and pressure applications. On the other end, the NIST REFPROP calculations are very accurate and can handle almost any situation but the computational cost is very high and the stability of these calculations is noticeably lower. For this reason, there’s no point in selecting a NIST based model when the physics of the application don’t require it. My experience is that most people tend to exaggerate real gas effects and are prone to overkill in fluid modeling. Note also that a poorly applied advanced model can introduce far more error than the effect you’re trying to correct for.
There is a wide spread of possible conditions that a given fluid might see in a particular class of design. For that reason, its import to know what the proper modeling approach is for the application. The figure below can serve as starting point that’s appropriate in most situations.
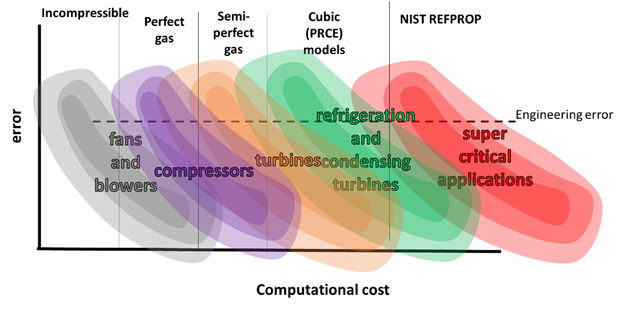
The figure is a rough guide and one can think of both the vertical and horizontal axis as logarithmic scales. Spot checks using higher order thermodynamic models can be very handy in giving piece of mind that the lower order models used in production runs are adequate.
The proper thermo model to apply is definitely worth some time thinking about. Using too simplistic a model can obviously lead to serious accuracy problems. Almost as bad is burning a lot of project time and budget using an advanced model that’s not needed. The Concepts NREC software has an entire spectrum of models available that will let you make the right choice for your application.